汽车空调滤清器粉尘过滤测试试验
1 范围
GB/T XXXX的本部分规定了测试空调滤清器对进入驾乘室空气中的污物(包括灰尘和花粉等)进行过滤的若干试验方法。本部分以此在实验室中评价或比较乘驾室空气滤清器和滤芯的性能。通过测试可给出滤清器的下述信息:压力降、分级过滤效率和储灰量等。
2 规范性引用文件
下列文件中的条款通过该标准的引用而成为本部分的条款。凡是注日期的引用文件,其随后所有的修改单(不包括勘误的内容)或修订版均不适用于本部分,然而,鼓励根据本部分达成协议的各方研究是否可使用这些文件的新版本。凡是不注日期的引用文件,其新版本适用于本部分。
ISO 12103-1:1997 道路车辆—滤清器评价用粉尘—第1部分:亚利桑那试验粉尘DIN EN 779:2002 一般通风用空气过滤器—过滤性能的测定DIN EN 1822-1:1998 高效空气过滤器(HEPA与ULPA)—第1部分:分级、性能测试、标识。
3 术语和定义
下列术语与定义适用于本标准。
3.1
试验空气流量 V test air flow rate
单位时间通过滤清器截面的试验空气体积。单位为每立方米每小时(m3/h)。
3.2
压力降 DPd pressure loss
滤清器上游和下游两侧的静压差。单位为帕(Pa)。
3.3
初始压力降DPA initial pressure loss
新的滤清器或滤芯两侧的压力降。单位为帕(Pa)。
3.4
终止压力降DPE final pressure loss
滤清器或滤芯在加灰程序结束后两侧的压力降。单位为帕(Pa)。
3.5
过滤面积 A filtration area滤清器或滤芯中起过滤作用的表面积。单位为平方米(m2
)。
3.6
分级过滤效率 fractional efficency按颗粒大小分级的过滤效率Ef(x)。
3.7
储灰量 G test dust-holding capacity根据8.3的测试程序,当达到商定的终止条件(如一定的压力降)时,在测试样件上捕获的测试粉尘的质量。单位为克(g)。
4 试验条件和测试物质
4.1 试验条件
4.1.1 空气状况
所吸入空气的温度必须为23°C±2°C,相对湿度为50%±3%。在测试滤清器的储灰量G的整个实验过程中,必须保持上述温度和湿度条件。试验条件的汇总见表C.2。
4.1.2 空气洁净
吸入装置内的空气必须经 EN 1822-1定义的至少H12级别的高效过滤器的过滤,而且在高效过滤器的前级需配置根据 EN 779 定义的 F7 或 F8 级别的中效过滤器。鉴于空气的净化要求和对试验设备的保护,建议在排气端安装类似的装置以捕获穿透测试样件的粉尘。
4.2 测试物
4.2.1 测试粉尘
测试粉尘使用 ISO 12103-1中定义的A2灰(细灰)或A4灰(粗灰)。试验前对试验粉尘应在105°C±5°C的条件下烘干4h后使用。
4.2.2 其他测试粉尘
针对特殊要求,也可采用其他测试粉尘/气雾剂,如氯化钾(KCl),单或多分散的乳胶球,植物花粉或其他粉尘等。在这种情况下,测试程序和试验条件应由滤清器制造商和使用者商定。
5 测试设备
5.1 基本构造
为完成该测试所需的试验装备的一个结构布置范例见图A.1至图A.5。图A.2中给出了主要部位的具体尺寸。这个装置,至少从加灰部分到出风面采样口,应该采用导电材料并接地。基本原则是尽量减少粉尘粒子的损失。符合规范的试验设备必须满足第5章和表C.1、表C.2的要求。
5.2 气流供给
供给气流需按4.1.2准备。在气流吸入装置后端的管道中要求安装流量调节装置,调节范围为150m3/h~680 m3/h。流量调节与滤清器上所加测试粉尘的量无关,并要求精确到±2%。要求从流量调节装置之后的气流输送管道密封。当管道内外压差达到500 Pa的情况下,所泄露的流量应小于100 l/min。气流导向部件的尺寸可根据实际情况进行选择。
5.3 测试通道
测试通道要求垂直布置。通过适当的措施,如添加导向板,确保气流在横向截面上均匀分布。图A.2所示。
5.4 试验加灰装置
5.4.1 加灰装置
选择加灰装置,使得根据4.2节选择的测试粉尘均匀供给。在测试过程中,要求该加灰装置不会改变测试粉尘原有的颗粒分布。
5.4.2 颗粒分布密度的稀释装置
测量分级过滤效率时,由于可能出现小颗粒粘合在一起从而被误统计为大颗粒,因此通过配备一个如图A.4所示的对不同大小的粒子具有选择性的稀释装置来降低粉尘的颗粒的分布密度。该装置安装在计量设备后的粉尘供给管上,而且可代替在粒子计数器前的稀释设备。做储灰量试验时,该稀释装置应关闭。
5.5 加灰
试验粉尘要求如图 A.2 所示那样逆气流方向导入。必须保证试验灰被均匀地分布在测试通道中。
测试通道必须采用导电材料,而吸入的气流必须干燥并不含油类物质。
一旦通过5.6至5.9的检测排除重要的采样错误,鉴于测试粉尘在立体空间中已均匀一致,就可以验证该测试系统的适用性。
5.6 采样管
采样管正对着空气流向安装。可以在测试样件的上下游分别安装采样管;或仅使用一个采样管安装在样件的下游位置,分别对安装了测试样件和不装测试样件两种情况进行测量。取样时,要求采样管内的气流速度尽可能地与采样管周围的气流速度一致(等速采样)。其偏差应控制在±20%以内。如果在测试样件的上下游各使用一采样管,要求这两个采样管属于同一规格型号,尤其需要满足5.9节中的要求。采样管必须位于管道截面的中心,而且与过滤器表面相距大约100 mm,若出现任何偏离,须经滤清器制造商和用户商定,并在试验报告中注明。
由于在滤清器上游和下游的粒子计数差异不是完全符合统计规律的(如系统误差和不可重复性),因此需要建立起相应的校正因子,对实际的测试结果进行校验。对于管道几何尺寸出现大的偏差的,同样需要进行校正。
5.7 连接管道
连接管道的布置要使因管道弯曲导致颗粒甩出或沉淀的粒子损失尽可能的小。这样的损失尤其对大颗粒试验物在数量上有影响。所有管道在满足输送悬浮物条件下,应尽可能地短且采用导电材料并接地。
5.8 粒子计数器
粒子计数器要求测量几何直径为0.3 ?m~10 ?m或空气动力学直径为0.5 ?m~15 ?m的粒子,并将之划分为至少六个等级。后一级要求记录所有大于10 ?m(几何直径)或15 ?m(动力学直径)的粒子数。因此,可以选择一款按照粒子的动力学直径或对应的几何直径进行分类的粒子计数器。粒子计数器和分级设备需要采用专用的具有特定分布的粒子校验,且每年至少校验一次。所选择的粒子计数器应在生产厂家的建议下使用。
每一类需要测试的特定尺寸的颗粒浓度与背景噪声之间的频度对比应大于50。
注:一个近似的几何学上的粒子直径换算公式为
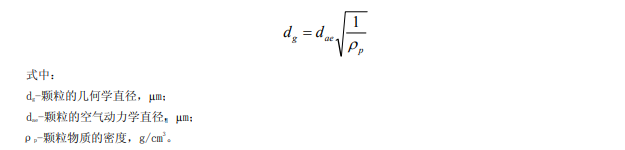
5.9 用作分级过滤效率测试的悬浮物在立体空间的均匀分布
测试条件:
流量:300 m3/h;
相对湿度:50%;
温度:23?C;
中空面板,其中空区域:200 mm×300 mm。
将上述中空区域等分为四个长方形区域。在该面板的中心上方以及四个等分矩形中心的上方分别至少测试五次颗粒的分布。要求在每一个确定的采样位置,从每一特定尺寸的分级通道记录的数值与平均值的偏差不应超过±5%。
上述调整表明,悬浮物供给稳定、分布均匀,从而保证了在测试样件的中心点取样代表性。
5.10 取样口位置
取样口位置如图A.2所示。
5.11 压差计
检测压差要求采用精密的测压仪器,如经标定的电子压力传感器,要求误差不超过±2%。
5.12 流量计
采用测试误差不超过2%的流量检测仪器。流量计的量程应不小于大可能检测流量的110%。
5.13 温度检测设备
温度的检测精度应满足试验条件,即23?C±0.5?C(在储灰量测试过程中,需要将安放测试设备的试验室温度控制在±2?C,见8.3节的注2)。
5.14 湿度计
相对湿度的检测要求应符合50%±1%。
5.15 称量设备
称量测试样件质量的天平精度要求达到±0.1 g。
6 测试装置状态确认
在开始滤清器的过滤试验之前,需要按照表C.2对测试装置进行状态确认。
为确认试验装置是否达到本标准的性能要求,须核对下列信息:
a)系统的的设计图纸及具体文档,包括:
1)粒子发生器;
2)内置颗粒物(可追溯);
3)粒子计数器的生产厂商、型号和校验数据;若配备稀释装置,同样需要上述信息。
b) 压差检测的校验数据;
c) 流量检测的校验数据;
d) 温度和湿度检测的校验数据;
e) 气流在给灰口和测试元件之间段空间的均匀同质性;
f) 颗粒分布的均匀同质性;
g) 颗粒浓度规格的要求,重合计数不得超过 5%;
h) 比较样件上游和下游颗粒浓度的测试数据,证明使用一个计数器或两个计数器对结果没有影响;
i) 数据证明,分级过滤器测试不会对滤清器储灰量造成大的影响;
j) 滤清器试验数据表明测试结果具有可重复性,如一些同质滤清器的测试序列或重复测试结果。
7 测试样件准备
滤清器总成和滤芯在试验中一律称为测试样件。样件要求是新的和干燥的,而且在试验前质量称量精确到0.1 g。
对双效过滤器的测试尚需按照试验条件进行长时间的稳定或预处理,直至相邻两次的质量称量没有变化(见8.3节的注2)。
8 测试程序
8.1 确定流量——初始压力降曲线
初始压降曲线通常针对特定流量进行检测,建议在额定流量的25%、50%、75%和%100处测量,也可由实验室和使用者商定。总的压力降扣除中空面板的压差即可得到测试样件两端的压力降。
8.2 确定额定流量下的分级过滤效率曲线
8.2.1 计算公式
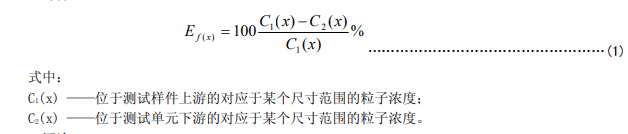
8.2.2 概论
为了正确地进行初始分级过滤效率的测定,需要注意以下几点:
- 测试通道需干净且密封良好;
- 测试仪器工作稳定且无间断;
- 取样探头和连接管道必需保持干净,而且连接管无破裂;
- 试验前调好粒子计数器;
- 测试样件外观应无缺陷,且安装密封良好。
8.2.3 试验程序
a)检查粒子计数器零点平衡;
b)将测试样件安装在检测设备上。注意边缘的密封情况;
c)分别在测试样件的上游和下游进行,各采样三次并取平均值作为检测结果。采样的间隙时间需长到足够清洗采样系统和测试设备至少两次。调节测试粉尘的浓度使得在每一次测试周期中,样件两端的压力降增加不超过 5%;
d)在试验记录中,记录分级过滤效率测试前后的压力降数值;
e)为避免粒子计数时的信号重迭,需要进行粉尘的稀释。特定尺寸颗粒的稀释因子需经实验确认;
f)确认粒子尺度-分级过滤效率曲线并记录。
8.3 确定滤清器的储灰量及对应的终端分级过滤效率
在某一确定流量,一定量的测试粉尘被引入测试通道。粉尘浓度必须保持在 75 mg/m3±3.75 mg/m3;测试粉尘的称量应精确到0.1 g。测试样件在加灰前称量一次,加灰到终止条件后再称量一次;两者的差额即为测试样件的储灰量。可以用加灰到预先设定的压力降作为终止条件。然后确定该储灰量下的阻力增量和分级过滤效率。
注:1. 沉积在测试样件装配平面或上游管道壁的粉尘允许不作处理,并在储灰量的计算中不作考虑。
注:2. 若采用同样的程序测试双效过滤器,需要考虑空气中的水蒸汽会被活性炭吸附或带走活性炭中的水分。复合材料所使用的化学物质、生产工艺等都会影响上述行为。因而,需要长时间地将测试样件在试验小室中稳定或预处理,直至它的质量维持恒定,即质量的变动小于1 g。通常要求的预处理时间为1.5 h,可依据具体情况调整。